Product Lifecycle Management
Product Lifecycle Management (PLM) refers to the concept of centralised product data management and process control that is integrated into all relevant company areas and serves as a ‘single point of truth’ along the entire product lifecycle. With this cross-departmental organisation, you can improve internal communication and coordination, handle customer order processes in a time and cost-saving manner and thus ensure the competitiveness of your company.
A digital product model
In the BDF PLM approach, the basis for efficient data management is a digital product model that is continuously enriched with data throughout all phases of the product life cycle.
Thanks to centralized and structured management, everyone involved in your company, from development and production to service or scrapping the product, has the same knowledge and redundancies or incorrect information can be avoided.
PLM promotes efficient planning and control of product information throughout the company and, by integrating the data into all relevant business processes, leads to a reduction in costs and careful use of resources.
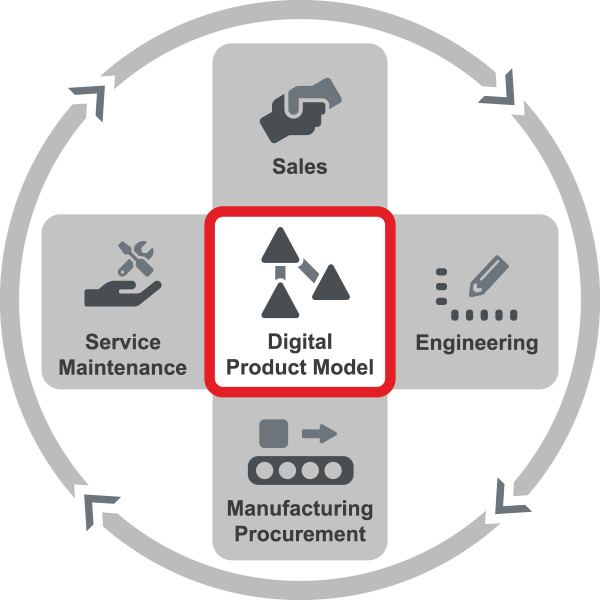
Our approach at BDF EXPERTS
SAP Product and Process Governance (SAP PPG) offers product lifecycle management that is fully integrated into SAP. By creating a digital product data model, all business processes relating to the product lifecycle can be controlled from SAP.
Comprehensive planning options with virtual objects and the integration of CAx data can be used as early as the product development stage.
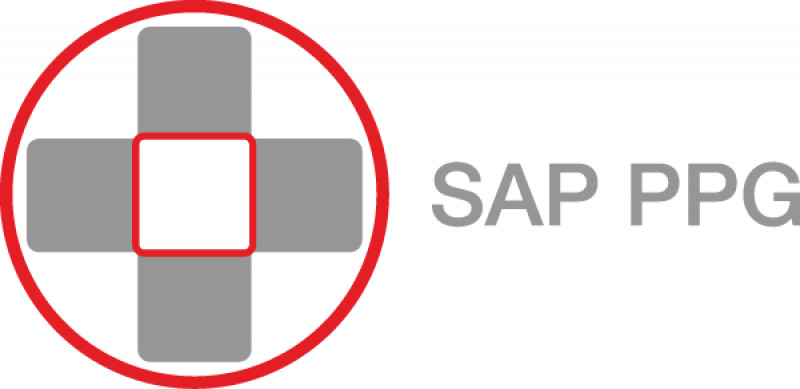
- With the Material Control Center (MCC), material masters can be created automatically and rule-based and parts lists can be generated.
- The Knowledge Control Center (KCC) offers the possibility of collecting and structurally mapping all product and configuration knowledge. Through integration in procurement, production, service & maintenance or the project system, additional objects such as purchase requisitions, production orders, technical location structures or WBS elements can be automatically generated and deadlines tracked.
- With BDF Simultaneous Costing (BDF SCC) in conjunction with Easy Cost Planning, you can also keep an eye on costs even in complex projects. Compare several forecast scenarios with each other, include current planned costs and derive targeted follow-up activities based on this in order to counteract deviations at an early stage.
- The Document Control Center (BDF DCC) also extends the document management system (DMS) and supports the planning, control, scheduling and dispatch of documents.
Structure management and configuration
Use templates, module libraries or guided structure copies for the simple and standardized creation of order-neutral or order-related structures with rule-based number assignment. For example,
- Product and document structures can be created, classified and inherit characteristic values.
- The structures can be created without master data and contain various views such as costs, deadlines, engineering, production, project assignment, service data, dispatch planning, etc.
- The master data can be generated directly from the structure in the further course of order processing.
Change management
Use the comprehensive change management functions in the PPG.
- Simple and complex multi-layer status networks in PPG.
- Integrated baseline management for change presentation.
- Change of all data generated with PPG with change number.
- Effectivity control based on the SAP change number.
Virtual objects
Use virtual objects such as virtual materials, documents, parts lists, work plans, equipment or functional locations when setting up various structures.
- The virtual objects can be planned in terms of content and filled and managed over the life cycle.
- This allows you to carry out extensive planning measures before the final objects exist or are generated.
- Costing data can also be maintained for a product structure in the early development phase.
- The planning items can then be filled with existing objects or new objects can be generated from them.
Knowledge management
Incorporate product and configuration knowledge directly into your product structures.
- With the help of knowledge management, configuration knowledge can be preconfigured and generated directly on a class- and object-dependent basis.
- By using the knowledge center in the PPG, this knowledge can be used directly in the SAP variant configuration.
- By using characteristic spaces and knowledge types, you always have an overview of the classes and objects used in the variant configuration and avoid redundancies.
Bill of materials
Derive your required Bill of materials directly from the PPG data.
- Material BOMs can be generated in the desired uses, sales order BOMs, project BOMs, equipment BOMs and functional location BOMs.
- This supports the Global Engineering and Global Production approach, in which production plants can be integrated in a global network via intercompany processes with the appropriate BOM type.
Configuration management
Map your configuration management with your project-related and project-neutral artifacts in the PPG structure.
- Artifacts can be reused in different orders and both the manufacturer's and the operator's perspective can be mapped.
- A baseline can be created for each PPG structure, which can be planned or unplanned and displayed and compared via the change cockpit.
- All aspects of configuration management are mapped with the integration into technical workstations and equipment.
Production/reprocessing integration
Generate planned orders, production orders, ERP routings and production BOMs directly from the PPG. In addition, production data packages can be configured using the SAP variant configuration. These can contain various production parameters and work instructions and can be transferred directly to the MES.
- In addition to production processes, reconditioning processes can also be mapped and recorded as maintenance files.
- Using the SAP variant configuration, the actual reprocessing scopes can be determined after the findings and transferred to the MES with the corresponding work plan and components.
- Thanks to integration in service and maintenance, equipment master records can be created, assigned or updated directly after reconditioning.
Project Costing
With PPG Project Costing, you can record the entire project costs across all phases (from quotation to project completion).
- Planned costs can already be planned in the quotation or product planning phase using the modular PPG - ECP (Easy Cost Planning) integration.
- With the quick cost estimate, a cost analysis can be created very efficiently via a simple input or via references to existing material masters, quotations, orders, etc.
If you want to create cost planning with reference to activity types, plants and a detailed costing sheet, ECP integration can be used. The planned costs are then transferred to various plan variants in PS and can also be evaluated across several PS structures via reporting (MIKA = simultaneous costing).