04.05.2022
Digitaler Zwilling im Service
Seit ziemlich genau zwei Jahrzehnten existiert der Begriff „Digitaler Zwilling“ bzw. „Digital Twin“ im Zusammenhang mit der fortschreitenden Digitalisierung im Maschinen- und Anlagenbau.
Was hat es mit diesem Begriff auf sich?
Das Wort „Zwilling“ ist eine Ableitung vom Zahlwort „zwei“ und bedeutet ursprünglich „was doppelt vorkommt“, „wovon es ein Zweites gibt“. Digitaler Zwilling bedeutet also, dass zu einem physischen Produkt ein virtuelles Gegenstück existiert.
Wie kommunizieren ein physisches und virtuelles Produkt?
Experten gehen heute davon aus, dass es im Jahre 2025 über 75 Milliarden Dinge (i.d.R. Komponenten/Produkte/Systeme) geben wird, die mit dem Internet verbunden sind. Für diese umfassende Vernetzung wurde bereits 1999 der Begriff Internet of Things (IoT) geprägt. Die über das Internet kommunizierenden physischen Produkte werden auch cyberphysische oder cybertronische Produkte genannt.
Der Begriff „Digitaler Zwilling“ wird also dahingehend erweitert, dass das physische Produkt und sein virtuelles Gegenstück durch einen kontinuierlichen Datenaustausch über das Internet miteinander verknüpft sind.
Ziel ist es dabei, neue service-orientierte Dienstleistungen anbieten zu können (z.B. vorbeugende Reparaturen im Rahmen einer Predictive-Maintenance-Strategie) und damit den Weg vom Internet of Things zum Internet of Services zu bahnen.
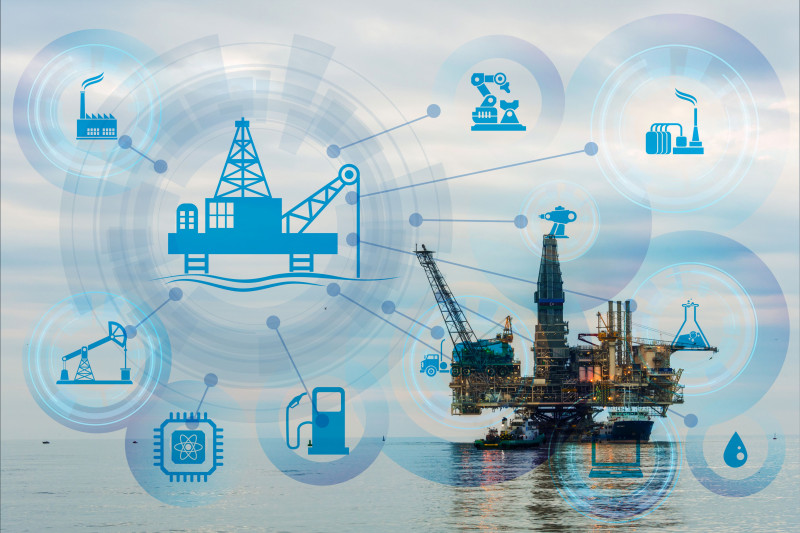
Wie hängen der digitale Zwilling und der Produktlebenszyklus zusammen?
Generell kann der Produktlebenszyklus in drei Hauptphasen strukturiert werden:
1. As-Designed-Phase:
- Die As-Designed-Phase umfasst die Phasen der Produktentwicklung und schließt mit der Produktionsfreigabe ab (Release for Production).
- Anmerkung: Produkte werden heute meist als Produktvarianten innerhalb einer Produktfamilie entwickelt; im Auftragsfall werden sie kundenspezifisch konfiguriert.
2. As-Built-Phase:
- Die darauf folgende As-Built-Phase beinhaltet die konfigurationsspezifische Herstellung einer Produktausprägung und reicht bis zur Produktübergabe in Kundenhand (Handover to Costomer).
- Das Ergebnis der As-Built-Phase ist das physische Produkt.
3. As-Maintained-/In-Service-Phase
- Abschließend begleitet die As-Maintained-/In-Service-Phase das Produkt über die verbleibende Lebensdauer.
- Dabei können sowohl vom Betreiber als auch vom Hersteller als auch von anderen Dienstleistungsanbietern Instandhaltungs- bzw. Serviceleistungen erbracht werden, um die geforderte Verfügbarkeit des physischen Produkts bzw. der physischen Anlage sicherzustellen.
Wie unterstützt SAP Software die oben genannten Anforderungen?
BDF EXPERTS berät seit über 20 Jahren Maschinen- und Anlagenbauer im Product Lifecycle Management, im Supply Chain Management sowie im Service und Asset Management mit SAP.
Aus den Erfahrungen im Beratungsgeschäft entwickelte BDF über die Jahre hinweg einen einzigartigen Lösungsansatz, um den Herausforderungen im Maschinen- und Anlagenbau zu begegnen. Mit Hilfe der von SAP vertriebenen SAP Product and Process Governance by BDF (SAP PPG) kann eine beliebig komplexe Produktstruktur in SAP abgebildet werden. Hierfür nutzt BDF unter anderem das integrierte Produkt- und Prozess Engineering (iPPE) von SAP und baut die Struktur in Form sogenannter iPPE-Knoten auf.
Bei der Produktprogrammplanung wird hierbei zunächst für alle Produkte eines Maschinen- oder Anlagenbauers eine Produktvariantenstruktur in der Template-Bibliothek aufgebaut, welche das Produkt inklusive aller möglichen Varianten hierarchisch abbildet.
Aus dieser 150%-Struktur wird bei Auftragseingang eine kundenspezifische Auftragsstruktur als 100%-As-Designed-Struktur ausgeleitet bzw. ggfs. weiter ausgearbeitet, die nicht nur die Materialstamm- und Produktstrukturdaten, sondern auch alle Dokumentationsdaten in Form von Dokumentinfosätzen im Sinne einer Produktkonfiguration enthält.
Neben der Unterstützung der As-Designed- und As-Built-Phase stellt SAP PPG auch Funktionen bereit, um aus der auftragsspezifischen As-Designed-Struktur heraus die Vorplanung Technischer Objekte (Technische Plätze und Equipments) und Objektstücklisten (Equipmentstücklisten) für die As-Maintained-/In-Service-Phase vorzunehmen.
Auf Basis dieser Planungsdaten werden zum definierten Zeitpunkt sowohl die Serviceobjektstruktur, bestehend aus hierarchisch aufgebauten Technischen Plätzen und eingebauten Equipments, als auch die zugeordneten Ersatzteillisten in Form von Equipmentstücklisten automatisiert ausgeleitet. Über kundenspezifisch festzulegende Logiken werden dabei aus der definierten kundenspezifischen Produktkonfiguration nur die servicerelevanten Positionen in die Ersatzteillisten und nur die servicerelevanten Dokumente in die Serviceobjektstruktur übernommen.
Damit entsteht der Digitale Zwilling für die As-Maintained-/In-Service-Phase quasi (halb-) automatisch aus der für Entwicklungs- und Fertigungszwecke kundenspezifisch aufgebauten Produktkonfiguration.
Welches SAP Produkt dient als IoT Enterprise Platform?
Damit nun nach erfolgter Inbetriebnahme das physische Produkt auf Betreiberseite mit seinem digitalen Zwilling auf Herstellerseite kommunizieren kann, und sowohl Hersteller als auch Betreiber Informationen austauschen können, ist eine IoT Enterprise Platform erforderlich.
Dazu bietet SAP die Cloud-Lösung SAP Asset Intelligence Network (AIN) an. Nach SAP bietet AIN „… eine digitale Plattform für die Zusammenarbeit bei der Equipment-Definition und -Instandhaltung. Es ermöglicht Geschäftspartnern, an einem gemeinsamen digitalen Zwilling über den gesamten Lebenszyklus von Anlagen hinweg zusammenzuarbeiten, was zu optimierten Instandhaltungsprozessen, einer besseren Anlagenleistung, einer Senkung der Betriebskosten und einem sichereren Betrieb führt.“
Nachdem der Hersteller die Serviceobjektstruktur inkl. der Ersatzteillisten und der servicerelevanten Dokumente auf SAP AIN publiziert hat, können die im Anlagenbetrieb gesammelten Daten von allen Kollaborationspartner genutzt werden, um die geforderte Anlagenverfügbarkeit sicherzustellen und Produkte und Prozesse gemeinsam und kontinuierlich zu optimieren.